
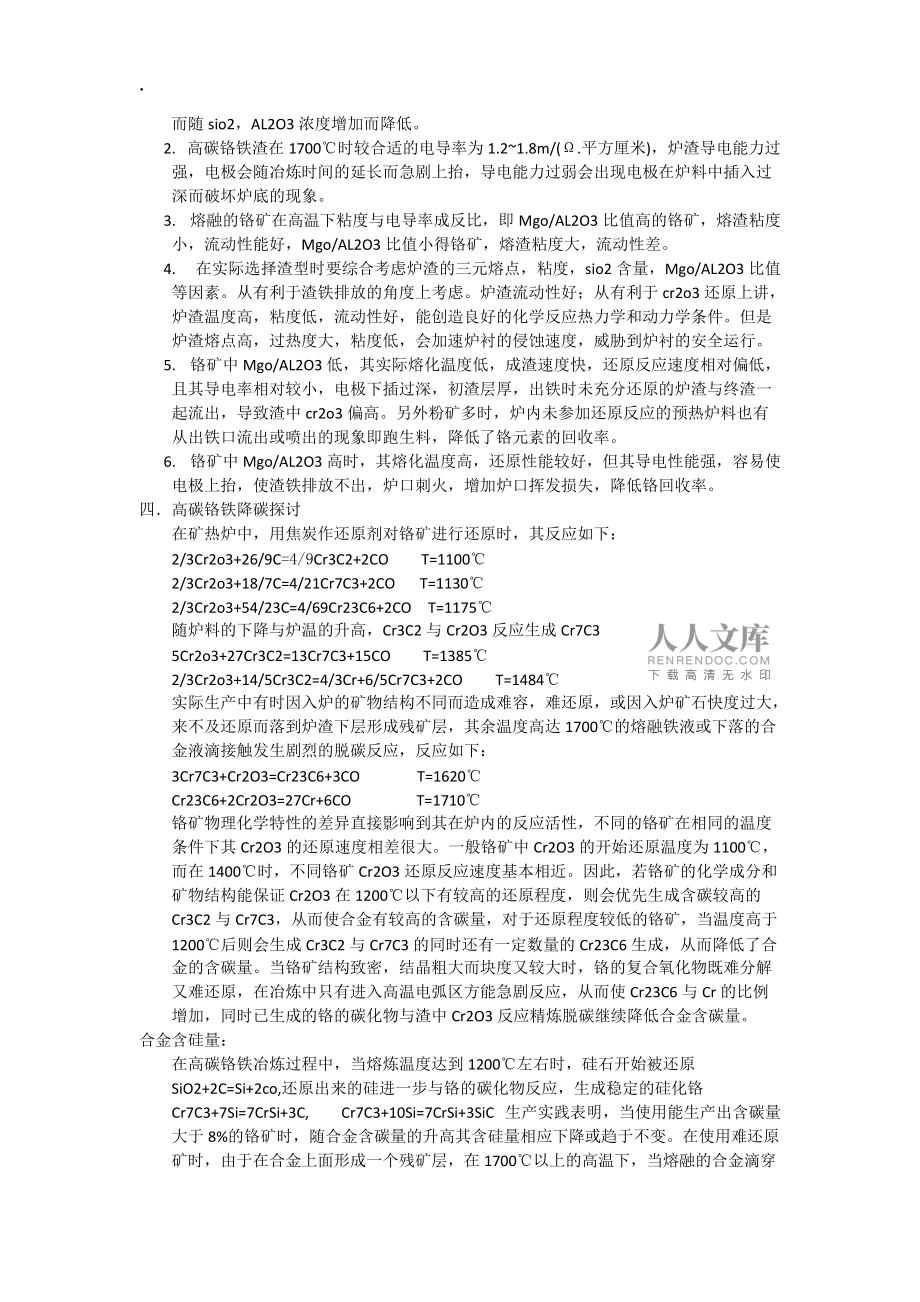



版權(quán)說明:本文檔由用戶提供并上傳,收益歸屬內(nèi)容提供方,若內(nèi)容存在侵權(quán),請進(jìn)行舉報或認(rèn)領(lǐng)
文檔簡介
1、.高碳鉻鐵合金降硫途徑探討一 硫的來源及存在狀態(tài)高碳鉻鐵中的硫來自于原料,其中焦炭和鉻礦帶入硫占絕大部分,焦炭中的硫以硫化物(FeS,CaS)或有機硫的形式存在,在實際生產(chǎn)過程中,原料中的硫有8%15%進(jìn)入合金,20%30%揮發(fā),60%70%進(jìn)入渣中,進(jìn)入合金的硫?qū)⑴c鉻生成一系列硫化物如:CrS, Cr2S3等。CrS在1565時熔化而不分解,低于800時分解生成Cr15S6.由于硫化物的熔點低于鉻鐵的熔點,所以這些硫化物分布于鉻鐵的表面上。二.降低高碳鉻鐵合金中硫含量主要有一下幾種途徑1 提高爐溫,以提高化學(xué)反應(yīng)的平衡常數(shù)2 降低渣中的cr2o3含量,生產(chǎn)過程中維持較高熔點操作Cr2o3含量
2、的高低反應(yīng)了有用元素的還原程度,較低的cr2o3含量意味著爐內(nèi)各項反應(yīng)進(jìn)行的較為徹底,還原劑焦炭過剩。在實際操作中,適當(dāng)控制爐渣熔點,避免過低熔點操作,保證還原劑用量充足,對脫硫效果較為有利。但爐渣熔點不宜過高,否則爐渣粘稠,渣鐵過熱,導(dǎo)致爐況惡化。3. 提高爐渣堿度,即增加渣中cao的含量,降低渣的粘度,增加爐渣的電導(dǎo)率,二者的增加都能夠改善爐內(nèi)反應(yīng)的動力學(xué)條件,保證爐內(nèi)功率分布均勻,擴(kuò)大坩堝,但同時也出現(xiàn)了電極消耗過快,爐墻掛渣減少,熱量損失等不利因素。4. 提高合金中c與si的百分含量,選用合適的鉻礦與控制合適的爐渣熔點5. 有時在鐵水包中加入石灰等脫硫劑也有一定的效果。6. 加石灰之后
3、,降低了熔渣的熔點,最終導(dǎo)致合金增碳,同時也降低了鉻回收率 原因分析:(1)石灰在成渣過程中與渣中Mgo,AL2O3形成鈣鋁黃長石,其熔點在1500左右,降低了還原溫度,使渣中cr2o3濃度增加,從而導(dǎo)致合金增碳。(2)由于石灰量的增加,使渣中cac2量增加,從而導(dǎo)致合金增碳。(3) caoMgoSiO2AL2O3四元渣系的脫硫能力遠(yuǎn)大于MgoSiO2AL2O3三元渣系,加石灰之后,能降低熔體的粘度及提高熔體電導(dǎo)率。(4)冶煉高碳鉻鐵采用四元渣時,渣中cao含量不宜控制過高,否則會引起負(fù)效應(yīng)。對于一定的熔渣,其電導(dǎo)率與粘度成反比,因此加石灰后,在使?fàn)t渣粘度降低的同時,能提高爐渣的電導(dǎo)率。二在實
4、踐中采用調(diào)整Mgo/AL2O3來調(diào)整鉻回收率 當(dāng)Mgo/AL2O3偏低時,可以配加白云石,菱鎂礦及廢鎂磚,增加渣中Mgo含量,提高M(jìn)go/AL2O3比值,提高爐渣溫度,以加快熔融爐料還原速度,使之與熔化速度相匹配。另外增大焦炭粒度與配比量,使?fàn)t料比電阻降低,同時可以增大爐內(nèi)焦炭層厚度增加未還原礦核穿過焦炭層的滯留時間,以提供更多的還原反應(yīng)機會,降低渣中cr2o3含量。 當(dāng)Mgo/AL2O3偏高時,增加硅石配入量,降低爐渣熔點,增加過熱度,增強流動性,使渣鐵正常排放。必要時,可以減小焦炭粒度能增加爐料比電阻,可以適當(dāng)減小焦炭層厚度,使電極下插較好,降低爐口料面溫度,防止翻渣,刺火發(fā)生,減少爐口揮
5、發(fā)損失,煙塵損失。三高溫下的導(dǎo)電率和粘度 1. 高碳鉻鐵爐渣的導(dǎo)電能力的大小取決于渣中離子數(shù)目的多少,熔渣的粘度增加,將會阻礙離子的遷移,從而降低導(dǎo)電度,熔渣的比電導(dǎo)隨堿性氧化物濃度的增加而增加,而隨sio2,AL2O3濃度增加而降低。 2. 高碳鉻鐵渣在1700時較合適的電導(dǎo)率為1.21.8m/(.平方厘米),爐渣導(dǎo)電能力過強,電極會隨冶煉時間的延長而急劇上抬,導(dǎo)電能力過弱會出現(xiàn)電極在爐料中插入過深而破壞爐底的現(xiàn)象。 3. 熔融的鉻礦在高溫下粘度與電導(dǎo)率成反比,即Mgo/AL2O3比值高的鉻礦,熔渣粘度小,流動性能好,Mgo/AL2O3比值小得鉻礦,熔渣粘度大,流動性差。 4. 在實際選擇渣
6、型時要綜合考慮爐渣的三元熔點,粘度,sio2含量,Mgo/AL2O3比值等因素。從有利于渣鐵排放的角度上考慮。爐渣流動性好;從有利于cr2o3還原上講,爐渣溫度高,粘度低,流動性好,能創(chuàng)造良好的化學(xué)反應(yīng)熱力學(xué)和動力學(xué)條件。但是爐渣熔點高,過熱度大,粘度低,會加速爐襯的侵蝕速度,威脅到爐襯的安全運行。 5. 鉻礦中Mgo/AL2O3低,其實際熔化溫度低,成渣速度快,還原反應(yīng)速度相對偏低,且其導(dǎo)電率相對較小,電極下插過深,初渣層厚,出鐵時未充分還原的爐渣與終渣一起流出,導(dǎo)致渣中cr2o3偏高。另外粉礦多時,爐內(nèi)未參加還原反應(yīng)的預(yù)熱爐料也有從出鐵口流出或噴出的現(xiàn)象即跑生料,降低了鉻元素的回收率。 6
7、. 鉻礦中Mgo/AL2O3高時,其熔化溫度高,還原性能較好,但其導(dǎo)電性能強,容易使電極上抬,使渣鐵排放不出,爐口刺火,增加爐口揮發(fā)損失,降低鉻回收率。四高碳鉻鐵降碳探討 在礦熱爐中,用焦炭作還原劑對鉻礦進(jìn)行還原時,其反應(yīng)如下: 2/3Cr2o3+26/9C=4/9Cr3C2+2CO T=1100 2/3Cr2o3+18/7C=4/21Cr7C3+2CO T=1130 2/3Cr2o3+54/23C=4/69Cr23C6+2CO T=1175 隨爐料的下降與爐溫的升高,Cr3C2與Cr2O3反應(yīng)生成Cr7C3 5Cr2o3+27Cr3C2=13Cr7C3+15CO T=1385 2/3Cr2o
8、3+14/5Cr3C2=4/3Cr+6/5Cr7C3+2CO T=1484 實際生產(chǎn)中有時因入爐的礦物結(jié)構(gòu)不同而造成難容,難還原,或因入爐礦石快度過大,來不及還原而落到爐渣下層形成殘礦層,其余溫度高達(dá)1700的熔融鐵液或下落的合金液滴接觸發(fā)生劇烈的脫碳反應(yīng),反應(yīng)如下: 3Cr7C3+Cr2O3=Cr23C6+3CO T=1620 Cr23C6+2Cr2O3=27Cr+6CO T=1710 鉻礦物理化學(xué)特性的差異直接影響到其在爐內(nèi)的反應(yīng)活性,不同的鉻礦在相同的溫度條件下其Cr2O3的還原速度相差很大。一般鉻礦中Cr2O3的開始還原溫度為1100,而在1400時,不同鉻礦Cr2O3還原反應(yīng)速度基本
9、相近。因此,若鉻礦的化學(xué)成分和礦物結(jié)構(gòu)能保證Cr2O3在1200以下有較高的還原程度,則會優(yōu)先生成含碳較高的Cr3C2與Cr7C3,從而使合金有較高的含碳量,對于還原程度較低的鉻礦,當(dāng)溫度高于1200后則會生成Cr3C2與Cr7C3的同時還有一定數(shù)量的Cr23C6生成,從而降低了合金的含碳量。當(dāng)鉻礦結(jié)構(gòu)致密,結(jié)晶粗大而塊度又較大時,鉻的復(fù)合氧化物既難分解又難還原,在冶煉中只有進(jìn)入高溫電弧區(qū)方能急劇反應(yīng),從而使Cr23C6與Cr的比例增加,同時已生成的鉻的碳化物與渣中Cr2O3反應(yīng)精煉脫碳繼續(xù)降低合金含碳量。合金含硅量: 在高碳鉻鐵冶煉過程中,當(dāng)熔煉溫度達(dá)到1200左右時,硅石開始被還原SiO2
10、+2C=Si+2co,還原出來的硅進(jìn)一步與鉻的碳化物反應(yīng),生成穩(wěn)定的硅化鉻Cr7C3+7Si=7CrSi+3C, Cr7C3+10Si=7CrSi+3SiC 生產(chǎn)實踐表明,當(dāng)使用能生產(chǎn)出含碳量大于8%的鉻礦時,隨合金含碳量的升高其含硅量相應(yīng)下降或趨于不變。在使用難還原礦時,由于在合金上面形成一個殘礦層,在1700以上的高溫下,當(dāng)熔融的合金滴穿過該殘礦層時,便發(fā)生激烈的脫碳反應(yīng),此時脫碳反應(yīng)遠(yuǎn)比硅的還原反應(yīng)劇烈,并且伴隨脫碳反應(yīng)的同時發(fā)生脫硅反應(yīng),3CrSi+2Cr2O3=7Cr+3SiO2,使生成的合金含碳量相對穩(wěn)定,且硅含量的提高對其影響不大。鉻礦的溶化性能和還原性能: 鉻礦的溶化性能是指鉻
11、礦熔化的難以程度,當(dāng)鉻礦中的鉻尖晶石的晶粒大,MgO/FeO比值大,高熔點物質(zhì)MgO,AL2O3多,以及鉻礦的脈石熔點高,則該礦就難熔。 鉻鐵的生成過程可以分為三個階段,鉻礦的還原主要在13001400進(jìn)行,這時的反應(yīng)物尚處于固體狀態(tài),因此鉻鐵還原過程屬于固態(tài)還原,還原劑與還原產(chǎn)物在鉻礦中的傳輸條件對反應(yīng)速度和反應(yīng)的完善程度影響大,這些條件是溫度,反應(yīng)界面,擴(kuò)散速度,傳輸距離及礦石晶格畸變等。 一般來說,具有致密結(jié)構(gòu)或密斑晶結(jié)構(gòu)及粗晶組織的塊狀鉻礦不易還原,MgO/AL2O3低的鉻礦難以還原,MgO/AL2O3比值高的礦易還原。 高碳鉻鐵電爐還原反應(yīng)分布:冶煉區(qū)域 反應(yīng)礦物 還原劑 溫度 反應(yīng)
12、方式預(yù)熱帶 Fe,MgCr,Al,Fe2O4,Fe3O4 CO, C 9001200 氣固軟熔帶 MgAl,Cr2O4+原礦 C 13001500 固固焦炭層,精煉層 MgAl,Cr2O4+原礦 FeCr7C3,C >1500 液固冶煉高碳鉻鐵的原料: 鉻礦中Cr2O340%,Cr2O3/FeO2.5 S<0.05% P<0.07% MgO與Al2O3含量不能過高,粒度10-70mm,如系難溶礦,粒度應(yīng)適當(dāng)小些。 焦炭要求固定碳不小于84%,灰分小于15%,S<0.6% 粒度3-20mm 硅石要求SiO297%,Al2O31.O% 熱穩(wěn)定性能好,不帶泥土,粒度20-80
13、mm 1. 合金中的鉻含量取決于鉻礦中的Cr2O3/FrO的比值和鉻回收率。一般使用Cr/Fe低的礦石生產(chǎn)出來的合金中鉻含量也低,使用Cr/Fe高的礦石生產(chǎn)出來的合金中鉻含量就高。為了生產(chǎn)鉻含量一定的合金,通常采用幾種Cr/Fe不同的礦石進(jìn)行冶煉,以達(dá)到調(diào)整、控制鉻含量的目的。有時,也可以在使用Cr/Fe高的礦石時配比部分廢鋼、鐵鱗或鐵礦來達(dá)到工藝要求2.合金中的碳含量主要與鉻礦的物理性能有關(guān),當(dāng)鉻礦易熔,塊度小時,化療速度快,爐溫底,合金含碳量高,反之若礦難熔,塊度大,化料速度慢,爐溫高,由于塊礦中Cr2O3對鉻的碳化物有精煉脫碳作用,合金含碳量低。金屬熔體中存在硅和碳的平衡。一般合金中碳含
14、量隨著硅含量的增加而降低,高碳鉻鐵的碳含量與冶煉工藝、使用礦種、爐渣組成有關(guān)。使用易熔礦且粒度較小時容易生產(chǎn)出碳含量偏高的合金,使用粒度大、密度大的難熔礦容易生產(chǎn)出含碳量較低的合金產(chǎn)品。爐渣中MgO/Al2O3增加到1以上時,合金中碳含量會增加、增加渣中CaO含量時,也容易得到含碳量較高的合金。一般,容量大、極心圓直徑大的電爐生產(chǎn)的高碳鉻鐵合金中碳含量偏低些。 3.合金中的硅含量主要與還原劑用量,爐渣中SiO2含量和爐溫有關(guān)。一般,還原劑用量多、爐溫高且爐渣中SiO2含量較高時,合金中的硅含量也高;反之,則合金中的硅含量較低。 4.在鉻鐵電爐中,初渣形成發(fā)生在鐵和鉻的還原之后,終渣是在焦炭層中
15、形成的,初渣在通過焦炭層時其化學(xué)組成和物理性質(zhì)均發(fā)生極大變化,終渣在爐內(nèi)對合金起一定的精煉作用,其組成與性質(zhì)基本上是穩(wěn)定的。 1t鐵合金多出0.5t爐渣時,爐渣所帶走的熱量僅使電耗增加4%左右,但其對爐況的影響就可使電耗猛增20%甚至更多。正常爐況的特征:1.三相電極深而穩(wěn)地插入爐料中,隨著爐料的不斷熔化,爐底存積的渣、鐵量的不斷增多,電極緩慢上抬;到冶煉后期要出鐵前,隨著熔池的不斷擴(kuò)大,三相電極電流平衡、穩(wěn)定,三相電極位置平穩(wěn)、平衡,易于操縱。2.冶煉過程中,隨著冶煉時間的增長,爐膛內(nèi)料面均勻下沉,三相電極周圍不刺火、不塌料、不翻渣。3冶煉過程中,爐膛內(nèi)爐料透氣性良好,無局部刺火、不冒白煙,
16、煙氣量少,較長的、橘黃色的火焰均勻地分布在整個爐料表面。4渣、鐵溫度正常,合金Cr、Si、C、P、S成分穩(wěn)定,波動小,渣中跑鉻低,Cr2O3含量在5%內(nèi),爐渣成份穩(wěn)定、波動小。5出鐵口好開易堵,渣、鐵溫度正常,排渣正常,出鐵順暢,渣、鐵分離好,不跑料、不夾雜。出鐵時間在5-10min之間。不正常爐況的特征:1. 還原劑量不足時,電極插入爐料內(nèi)過深,各相電極負(fù)荷波動較大、電極消耗快,冶煉中后期電極周圍翻渣現(xiàn)象嚴(yán)重、形成的渣殼較硬,化料速度減慢、爐口火焰發(fā)暗。成品合金含硅量偏低、還原劑嚴(yán)重不足時成品合金含碳量也明顯降低,產(chǎn)品表面泡多、硬度大,不易破碎加工,爐渣粘稠,不易從爐內(nèi)排出,渣、鐵分離不好,
17、渣中跑鉻多。2. 還原劑過剩時,電極下插淺且容易上抬,各相電極負(fù)荷波動大,電極消耗慢,電極四周火焰增長、易跑火或冶煉中后期翻渣嚴(yán)重,形成較大的渣殼,但渣殼較疏松、易碎。爐底溫度低,出鐵口不易打開,爐渣不易從爐內(nèi)排出,爐口火焰短且呈淺藍(lán)色,成品合金含硅、碳量均有較明顯的升高。產(chǎn)品易破碎加工,渣中Cr2O3含量少。3. 硅石用量不足時,爐渣粘稠流動性差,電極下插淺、爐口溫度高,電極四周有粘稠的渣子、易刺火、易翻渣、爐渣粘度大,不易從爐內(nèi)排出。由于爐溫過高造成鐵水過熱,成品合金中含硅量偏高、含碳量偏低,渣鐵數(shù)量均少。4. 硅石用量過多時,電極下插較深,爐口火焰發(fā)暗,渣稀、流動性好、渣中SiO2含量高
18、,凝固的渣子表面發(fā)黑并顯得很粗糙。爐墻(襯)腐蝕嚴(yán)重、爐眼變大。出鐵鑄錠表面塔鐵現(xiàn)象嚴(yán)重,成品合金中含碳量升高,含硅量偏低。因爐溫偏低,液態(tài)的合金過熱度小,不易從爐內(nèi)排出、渣多鐵少。渣中Cr2O3含量偏高。5. 硅石與焦炭都不足時,爐渣中SiO2含量低,很粘稠,含有許多未被還原的鉻粒和小金屬粒,不易從爐內(nèi)流出,合金中中硅和碳的含量均有降低。6. 焦炭不足,硅石量過剩時,爐渣溫度低,易熔而粘稠,含有大量的SiO2,Cr2o3,FeO,合金中硅含量下降,碳含量上升,電極下插深,消耗增加。7. 硅石與焦炭過剩時,爐渣易熔,從出鐵口排出一些掛渣的焦炭,合金中硅和碳量都高,電極下插不穩(wěn)。8. 焦炭過剩,
19、硅石不足時,電極上抬,出現(xiàn)刺火,焦炭自坩堝里噴出,爐渣熔點高,渣的溫度也高,渣中Cr2O3含量低,爐渣粘稠,不易從爐內(nèi)放出。 溶劑用量影響爐渣成分,爐渣成分決定爐渣熔點,爐渣熔點決定爐內(nèi)溫度。 爐渣的熔點隨SiO2量的增加而下降,若渣中SiO2含量過高,爐渣的比電阻下降,電極不能深插,爐渣過熱少,鐵水溫度低。渣中Al2O3含量過高,爐渣粘度增加,不利于排渣,但Al2O3能增加爐渣電阻率,有利于電極深插。 金屬熔體中存在硅與碳的平衡,碳含量隨硅含量的增加而減少。 在高碳鉻鐵生產(chǎn)中,爐渣中SiO2含量是由合適的爐渣熔點1923K到1973K決定的,降低合金含硅量的措施并非是降低渣中SiO2活度,而
20、是增加渣中SiO2含量,從而大幅度降低體系的熔點,從而抑制了硅的還原。 改善爐渣流動性會提高反應(yīng)物的擴(kuò)散能力,從而增大脫硫速度,提高爐溫與有助于降低合金含硫量。高碳鉻鐵冶煉中的硅行為淺析1. 高碳鉻鐵冶煉過程中合金含硅量的變化規(guī)律:在高碳鉻鐵冶煉過程中,其合金含硅量實際上只帶表兩次出鐵間隔中積聚在爐缸下部鐵水的平均含硅量,而冶煉過程中爐內(nèi)不同區(qū)域的金屬含硅量并不相同。 合金含硅升高區(qū)域:從散料層開始到熔融層和殘焦層交界處為止,隨著金屬顆粒向爐缸深處下沉,合金含硅量不斷上升。 合金含硅下降區(qū)域:從熔融層和殘焦交界層開始到出鐵口為止 合金含硅不穩(wěn)區(qū)域:指爐底積鐵層,對于同一電爐在一定時間范圍內(nèi),該
21、層鐵水含硅量基本穩(wěn)定,但由于礦種的不同,隨時間的變化和積鐵層厚度的變化,其含硅量有所變化,固稱之為含硅不穩(wěn)定區(qū)域。2. 高碳鉻鐵冶煉過程中合金含硅量變化的影響因素:高碳鉻鐵冶煉過程中合金中的硅來源于礦石中的SiO2和溶劑硅石,其具體反應(yīng)如下:1/2SiO2+C=1/2Si+CO SiO2+C=SiO+COSiO+C=Si+CO以上各反應(yīng)在爐內(nèi)不同區(qū)域的反應(yīng)程度有所不同,SiO2的還原在殘焦層和熔渣區(qū)進(jìn)行較快,當(dāng)熔融的合金液滴在高溫下通過熔渣區(qū)下部的礦石層時,發(fā)生脫硅反應(yīng)。殘礦層區(qū)域是脫硅反應(yīng)區(qū),通過該區(qū)合金含硅量有所下降。 硅石配入量對合金含硅量的影響:(隨料批中硅石的配入量增加,合金含硅量先
22、增大,后減小,我們習(xí)慣把增大的區(qū)域叫做A區(qū),減小的區(qū)域叫做B區(qū))在A區(qū),隨硅石配入量的增加合金含硅上升,說明反應(yīng)物濃度不夠,也就是SiO2活度小,雖然溫度達(dá)到要求,但反應(yīng)物受限。在B區(qū),隨硅石配入量增加,爐渣熔點降低,爐溫下降,這樣隨硅石配入量的增加合金含硅下降,該區(qū)域爐溫成了反應(yīng)的限制性環(huán)節(jié)。在實際冶煉過程中,首先要確定峰值時硅石的配入量,峰值的確定一般在理論焦炭配入量不變的情況下,變動硅石配入量來確定。實際經(jīng)驗表明,硅石配入量確定在B區(qū)內(nèi),并為峰值配入量的120%130%范圍內(nèi),這樣只要調(diào)整焦炭這一單變量即可控制合金含硅量,如果確定在A區(qū),則合金含硅波動較大,爐前,路上操作十分困難,技術(shù)指
23、標(biāo)很不理想。 焦炭配入量對合金含硅量的影響:焦炭作為高碳鉻鐵冶煉的還原劑,一般隨料批中焦炭配入量的增加,合金含硅量上升,因為焦炭配入量增加有利于提高爐溫和SiO2與C的反應(yīng),還原出來的硅量增加,一部分取代合金中的碳。反之焦炭用量不足,則合金含硅量下降。在實際冶煉操作中此規(guī)律適應(yīng)于B區(qū)。當(dāng)溶劑硅石量不足時,隨焦炭配入量增加,合金含硅量達(dá)到一定數(shù)值后將不再增高。 鉻礦特性對合金含硅量的影響:鉻礦對合金含硅量的影響主要是礦中氧化物的含量。MgO,CaO堿性氧化物都有降低合金含硅量的作用。原因是堿性氧化物都能與SiO2形成硅酸鹽化合物,降低了渣中SiO2活度,使合金含硅量受到一定限制。在使用MgO及堿
24、性氧化物含量較高的鉻礦時,硅石配入量要適當(dāng)增加,以增加SiO2活度使合金含硅量得以保證。鉻礦中Al2O3對合金含硅量有升高的作用,原因是Al2O3含量高,晶粒大,屬于難還原的鋁鉻鐵礦,Al2O3的增加使?fàn)t渣和爐料的導(dǎo)電性變差,電極深插,有利于SiO2的還原。此時可以配部分白灰溶劑,增加其爐渣導(dǎo)電性,對合金含硅有很大的抑制作用,另外還可以增加爐渣的流動性。 合金含碳量對合金含硅量的影響:在鉻礦確定的條件下,高碳鉻鐵冶煉過程中爐內(nèi)各區(qū)域大致呈現(xiàn)硅低則碳高,碳高則硅低的規(guī)律。表明合金含硅量受含碳量的影響。高碳鉻鐵電爐爐襯的損壞及維護(hù)爐襯的損壞在冶煉中是不可避免的,但爐襯各部位的損壞速度是不一致的,爐底,爐缸(儲鐵層和渣線)出鐵口等重要部位損壞較快,降低了爐襯壽命。這些部位的損壞與耐火材料質(zhì)量及選擇,所處的環(huán)境有直接關(guān)系,從有關(guān)數(shù)據(jù)表明改進(jìn)耐火材料質(zhì)量對鐵合金爐襯壽命的貢獻(xiàn)越來越低,而改善耐火材料所處環(huán)境會減緩其損壞速度,從而延長爐襯壽命。爐襯損壞的影響因素:1. 物理作用:耐火材料熔損:在靠近電弧高溫區(qū)的耐火材料,工作溫度超過其耐火度后就會發(fā)生耐材熔損。 機械沖刷:在強大的弧光和電磁攪拌作用下爐渣與鐵水激烈運動,不停沖刷,如爐底,爐缸鎂磚軟化的工作層
溫馨提示
- 1. 本站所有資源如無特殊說明,都需要本地電腦安裝OFFICE2007和PDF閱讀器。圖紙軟件為CAD,CAXA,PROE,UG,SolidWorks等.壓縮文件請下載最新的WinRAR軟件解壓。
- 2. 本站的文檔不包含任何第三方提供的附件圖紙等,如果需要附件,請聯(lián)系上傳者。文件的所有權(quán)益歸上傳用戶所有。
- 3. 本站RAR壓縮包中若帶圖紙,網(wǎng)頁內(nèi)容里面會有圖紙預(yù)覽,若沒有圖紙預(yù)覽就沒有圖紙。
- 4. 未經(jīng)權(quán)益所有人同意不得將文件中的內(nèi)容挪作商業(yè)或盈利用途。
- 5. 人人文庫網(wǎng)僅提供信息存儲空間,僅對用戶上傳內(nèi)容的表現(xiàn)方式做保護(hù)處理,對用戶上傳分享的文檔內(nèi)容本身不做任何修改或編輯,并不能對任何下載內(nèi)容負(fù)責(zé)。
- 6. 下載文件中如有侵權(quán)或不適當(dāng)內(nèi)容,請與我們聯(lián)系,我們立即糾正。
- 7. 本站不保證下載資源的準(zhǔn)確性、安全性和完整性, 同時也不承擔(dān)用戶因使用這些下載資源對自己和他人造成任何形式的傷害或損失。
最新文檔
- 遺傳病遠(yuǎn)程診斷技術(shù)的創(chuàng)新與應(yīng)用-洞察分析
- 2025年人教版(2024)八年級地理上冊階段測試試卷
- 2025年新科版九年級生物上冊階段測試試卷
- 2025年度美團(tuán)商家入駐合同及運營支持細(xì)則4篇
- 維修服務(wù)模式創(chuàng)新-洞察分析
- 2025年人教新起點九年級物理下冊月考試卷含答案
- 2025年上教版七年級生物上冊月考試卷
- 2025年外研版三年級起點九年級歷史上冊階段測試試卷含答案
- 銀幣收藏投資策略-洞察分析
- 鞋履新材料應(yīng)用趨勢分析-洞察分析
- 物業(yè)民法典知識培訓(xùn)課件
- 2023年初中畢業(yè)生信息技術(shù)中考知識點詳解
- 2024-2025學(xué)年山東省德州市高中五校高二上學(xué)期期中考試地理試題(解析版)
- 《萬方數(shù)據(jù)資源介紹》課件
- 麻風(fēng)病病情分析
- 《急診科建設(shè)與設(shè)備配置標(biāo)準(zhǔn)》
- 第一章-地震工程學(xué)概論
- JJF(陜) 063-2021 漆膜沖擊器校準(zhǔn)規(guī)范
- 《中國糖尿病防治指南(2024版)》更新要點解讀
- TSGD7002-2023-壓力管道元件型式試驗規(guī)則
- 2024年度家庭醫(yī)生簽約服務(wù)培訓(xùn)課件
評論
0/150
提交評論